Maxterial's H-Max Coating Surpasses Hard Chrome in Performance and Environmental Impact
November 20th, 2024 8:00 AM
By: FisherVista
Maxterial Inc. has developed H-Max, a coating technology that outperforms hexavalent chrome while being safer and more environmentally friendly. This breakthrough could significantly reduce industrial carbon emissions and eliminate hazardous chemicals from manufacturing processes.
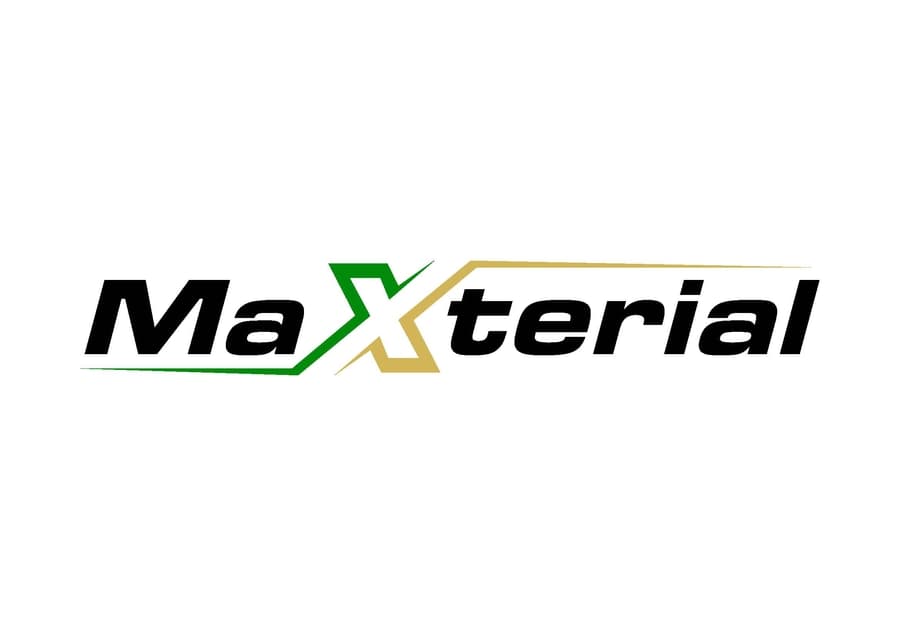
Maxterial Inc., a venture capital-backed advanced chemical and coating technology company, has announced a major breakthrough in industrial coatings. Their H-Max product line has demonstrated superior performance to hard hexavalent chrome, a long-standing industry standard known for its durability but also for its carcinogenic properties and environmental hazards.
The development of H-Max represents a significant leap forward in addressing a challenge that has long plagued the steel industry and many other manufacturing sectors. For decades, hexavalent chrome has been the go-to coating for high-wear manufacturing parts, despite its known health risks and heavy regulation. Previous attempts to replace it have typically fallen short in terms of performance, scalability, or cost-effectiveness. H-Max, however, appears to have broken this cycle by offering superior performance across major specifications while maintaining a reasonable total cost of ownership for original equipment manufacturers (OEMs).
Maxterial's Chief Technology Officer and CEO presented compelling results at several industry conferences in 2024, including AISTech, IVT EXPO, and ASETSDefense. The company conducted 27 different tests, with one notable trial involving the coating of cold rolling work rolls for a global steel production company. These coated rolls were subjected to extreme wear 'torture tests' under high pressure, conditions under which chromium and previous chrome replacements had failed. H-Max not only succeeded in these tests but also showed potential for significantly increasing the lifetime of parts, which could lead to reduced downtime in steel production processes.
The implications of this technology extend far beyond simply replacing a hazardous material. According to studies by Argonne National Laboratory, approximately 23% of the world's total energy consumption is attributed to tribological contacts, with 3% specifically devoted to remanufacturing worn parts and equipment replacement. The adoption of advanced tribological solutions like H-Max could contribute to saving up to 3,140 Mt of CO2 per year. This dual benefit of superior performance and substantial carbon reduction positions H-Max as a potential game-changer in industrial sustainability efforts.
While comprehensive testing in actual steel mills and large production lines is still pending, H-Max has already found applications in hydraulic parts, leveling rolls, and casting molds where less wear resistance is required. The technology's success is attributed to Maxterial's unique approach, which couples breakthrough technologies with a proprietary on-site replacement system.
The development of H-Max is particularly noteworthy given the backing Maxterial has received from prominent investors, including Peter Thiel's Breakout Labs and the corporate venture capital arms of multinational companies such as Saint-Gobain, Anglo American, and Ciech. This support underscores the potential impact of the technology across various industries.
As industries worldwide seek to reduce their environmental footprint and improve operational efficiency, technologies like H-Max offer a promising path forward. By addressing both performance and sustainability concerns, Maxterial's innovation could accelerate the transition away from hazardous materials in manufacturing processes. The company's collaborative approach to research and development, working closely with implementation partners and manufacturing teams, suggests that H-Max could be rapidly adopted across multiple sectors.
The success of H-Max in outperforming hexavalent chrome marks a significant milestone in materials science and industrial coating technology. As more comprehensive trials are conducted and the technology is implemented on a larger scale, it has the potential to transform manufacturing processes, reduce industrial carbon emissions, and set new standards for environmentally responsible innovation in the materials science industry.
Source Statement
This news article relied primarily on a press release disributed by 24-7 Press Release. You can read the source press release here,
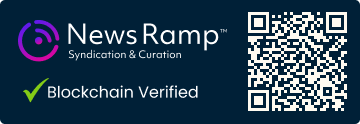